5S: O que é, passo a passo para aplicar na sua empresa e exemplos
18 min de leitura

Tallis Gomes
15 de fev. de 2024 • Última atualização 23 de jan. de 2025 • 18 min de leitura
O sistema 5S é uma metodologia de origem japonesa, projetada para melhorar a eficiência e a qualidade no ambiente de trabalho, especialmente em setores industriais.
Organizar as diferentes etapas do trabalho faz parte de todos os manuais de eficiência e ocupa um espaço importante na metodologia enxuta (lean), que busca otimizar o valor entregue ao cliente. Combinada aos princípios do lean, o sistema 5S classifica, organiza, limpa, padroniza e mantém a cultura que busca a excelência na melhoria diária.
O 5S é uma metodologia central da lean manufacturing, a chamada manufatura enxuta, e foi implementada pela primeira vez no Sistema de Produção da Toyota (TPS) na década de 1960. De lá para cá, o 5S ganhou o mundo e tem sido aplicado para maximizar a eficiência, eliminar o desperdício, melhorar o flow e reduzir o número de processos ao mínimo necessário. No final, o resultado é um ambiente de trabalho limpo e organizado.
Leia mais: Kaizen - o que é, como aplicar na sua empresa e exemplos
A seguir, vamos explicar melhor o conceito de 5S, como surgiu, como é aplicado nas empresas e um passo a passo para implementar no seu negócio.
O que é o 5S?
5S é uma metodologia focada na organização do local de trabalho com o objetivo de otimizar a eficiência e a produtividade – eliminando desperdícios, melhorando a segurança e aprimorando a eficiência operacional. A metodologia teve origem no Japão e está intimamente associada ao Sistema Toyota de Produção (TPS).
A metodologia 5S foi popularizada por empresas japonesas como parte de suas iniciativas de manufatura enxuta, que incluem ainda conceitos como Kaizen, Kanban e Poka Yoke, entre outros. Embora suas raízes estejam na produção industrial, os princípios do 5S têm sido aplicados com sucesso em vários setores e indústrias para melhorar a eficiência, a segurança e a organização geral do local de trabalho.
O sistema 5S não só ajuda a reduzir o tempo que não agrega valor, mas também melhora a produtividade e a qualidade. O 5S oferece uma estrutura para organizar e manter um local de trabalho limpo, organizado e eficiente.
Leia mais: Poka Yoke - O que é, como funciona e exemplos
O nome 5S vem de cinco palavras japonesas, cada uma começando com "S", para definir etapas fundamentais na jornada rumo à excelência no local de trabalho. Os cinco “S”s significam:
1. Seiri: Senso de Utilização
Seiri, ou senso de utilização, é o primeiro passo no sistema 5S, focando na eliminação de itens desnecessários no ambiente de trabalho. A prática do Seiri não só libera espaço físico, mas também reduz o tempo gasto na procura de ferramentas e materiais, simplificando os processos operacionais.
Como Implementar o Seiri?
- Identificação de Itens Desnecessários: Realize auditorias regulares para identificar ferramentas, materiais e equipamentos que não são utilizados frequentemente.
- Criação de um Sistema de Etiquetagem: Utilize etiquetas coloridas para marcar itens como necessários, desnecessários ou para revisão.
- Descarte ou Reciclagem Apropriada: Estabeleça métodos para descartar ou reciclar itens que não são mais necessários.
2. Seiton: Senso de Ordenação
O Seiton, ou senso de ordenação, envolve a organização de todos os itens de maneira eficiente e lógica. O objetivo é minimizar o tempo de busca, garantindo que cada item tenha um lugar específico e seja facilmente acessível.
Estratégias para o Seiton:
- Layouts Eficientes: Desenvolva layouts que reduzam o movimento desnecessário e coloquem os materiais mais utilizados mais próximos do local de uso.
- Sinalização Clara: Implemente sinalizações visuais claras para indicar onde cada item deve ser guardado.
- Manutenção da Ordem: Encoraje todos os funcionários a devolverem os itens para o seu lugar após o uso.
3. Seiso: Senso de Limpeza
O Seiso, ou senso de limpeza, é crucial não apenas para a manutenção da segurança, mas também para a prevenção de falhas de equipamentos e a promoção de um ambiente de trabalho mais agradável.
Implementando o Seiso:
- Rotinas de Limpeza Diárias: Estabeleça rotinas de limpeza no início e no fim de cada turno.
- Checklists de Limpeza: Crie checklists detalhados para áreas e equipamentos específicos, garantindo que nada seja negligenciado.
- Treinamento Contínuo: Assegure que todos os funcionários estejam treinados nas práticas de limpeza e entendam sua importância.
4. Seiketsu: Senso de Padronização
O Seiketsu foca na padronização dos primeiros três 'S', garantindo que as práticas de utilização, ordenação e limpeza sejam consistentemente aplicadas.
Como Padronizar:
- Documentação das Práticas: Documente todas as práticas e procedimentos relacionados ao 5S.
- Auditorias Regulares: Realize auditorias para garantir que as práticas estejam sendo seguidas.
- Feedback e Melhoria Contínua: Utilize o feedback dos funcionários para melhorar continuamente os processos.
5. Shitsuke: Senso de Disciplina
Shitsuke é o último 'S', enfatizando a disciplina e o comprometimento com a manutenção dos padrões estabelecidos.
Estratégias para Fortalecer o Shitsuke:
- Cultura de Responsabilidade: Promova uma cultura onde cada funcionário se sinta responsável pela manutenção dos padrões do 5S.
- Reconhecimento e Recompensas: Implemente um sistema de recompensas para reconhecer os funcionários que exemplificam excelentes práticas do 5S.
- Treinamento e Educação Contínuos: Assegure que novos funcionários recebam treinamento adequado sobre o sistema 5S e que o treinamento seja atualizado regularmente.
Nos últimos anos, um sexto “S” foi adicionado a essa abordagem para incluir a segurança.
Framework 5S (Crédito: G4 Educação)
Como surgiu o 5S?
A metodologia 5S surgiu no Japão como um aprimoramento do Sistema Toyota de Produção (TPS), que foi desenvolvido por Taiichi Ohno, Eiji Toyoda e outros engenheiros industriais japoneses entre 1948 e 1975. No redesenho, que contou com a contribuição de Sakichi Toyoda (fundador da Toyota, considerado o “pai da revolução industrial japonesa”), o TPS evoluiu e foi batizado como 5S.
A metodologia 5S carrega os ensinamentos e contribuições de diversas pessoas.
- Shigeo Shingo. Engenheiro japonês que considerava o 5S a pedra angular de uma produção eficiente e estável. Segundo ele, o 5S não era um fim e sim um meio de melhorar a produtividade e aumentar a qualidade.
- Hiroyuki Hirano. Extensão dos trabalhos anteriores de Hirano sobre sistemas de produção Just-in-Time (JIT), o 5S foi popularizado como “um processo contínuo que deve ser mantido”. Ele desenvolveu um framework para o 5S e escreveu uma série de manuais sobre a metodologia, incluindo “5S for Operators: 5 Pillars of the Visual Workplace (For Your Organization)”.
- Takashi Osada. Ao simplificar os conceitos da metodologia 5S, Osada contribuiu para tornar o conceito mais acessível, como em “The 5S's: Five Keys to a Total Quality Environment”.
Leia mais: O que é Lean Startup, o conceito que todo empreendedor deveria conhecer
O impacto do 5S no espaço de trabalho
Manter seu espaço de trabalho organizado e limpo tem a ver com um conceito enraizado na cultura japonesa e que está presente no design minimalista, na decoração esparsa das casas tradicionais, no cumprimento e exatidão das rotinas diárias. Organização e limpeza são vistos como pilares da “serenidade”.
Partindo da ideia de que apenas o necessário tem lugar, é mais fácil se concentrar e entrar no “flow” do trabalho.
O conceito de “Ma” é um bom ponto de partida: o uso intencional do espaço que valoriza o vazio tanto quanto a plenitude. O resultado visual é um ambiente mais cuidadoso e calmo.
Ao organizar uma casa, por exemplo, o "Ma" incentiva:
- A organização para remover itens desnecessários, permitindo um espaço mais aberto.
- Incorporar espaço negativo criando intervalos entre os objetos para permitir que o olho descanse.
- Alcançar o equilíbrio espacial organizando os móveis de forma a equilibrar o espaço. Para fazer isso, evite a superlotação, deixando áreas abertas suficientes para criar uma sensação de fluxo. Isso também se aplica à criação de caminhos abertos em um cômodo.
- Criar zonas funcionais em um espaço.
No caso do 5S, o método traz como resultado:
- Aumento da produtividade e da eficiência devido à redução do desperdício e à simplificação dos processos.
- Melhoria da qualidade e da confiabilidade dos produtos ou serviços por meio de práticas padronizadas e melhor organização.
- Aumento da segurança e da limpeza do local de trabalho, resultando em menos acidentes e lesões.
- Economia de custos com a redução de estoques, menores custos de manutenção e melhor utilização de recursos.
- Maior moral, envolvimento e satisfação dos funcionários como resultado de um ambiente de trabalho mais limpo e organizado.
- Maior satisfação do cliente devido a tempos de resposta mais rápidos, menos erros e maior qualidade do produto/serviço.
- Seguindo a metodologia 5S e refinando continuamente suas práticas, as empresas podem criar uma cultura de local de trabalho focada em excelência, eficiência e melhoria contínua.
5S: Por que usar e quais são os benefícios
A metodologia 5S oferece uma abordagem estruturada para a organização do local de trabalho e a melhoria contínua, permitindo que as empresas alcancem níveis mais altos de eficiência, qualidade e segurança em vários setores e ambientes. Os benefícios da aplicação da metodologia 5S incluem:
- Aumento da eficiência. Ao eliminar o desperdício e otimizar os fluxos de trabalho, as empresas podem realizar tarefas mais rapidamente e com menos recursos, o que leva ao aumento da produtividade e da lucratividade.
- Melhoria da qualidade. Espaços de trabalho organizados e processos padronizados reduzem a probabilidade de erros e defeitos, resultando em produtos e serviços de maior qualidade.
- Segurança aprimorada. Ambientes de trabalho limpos e bem organizados são mais seguros para os funcionários, reduzindo o risco de acidentes e lesões. Os procedimentos padronizados também contribuem para um local de trabalho mais seguro, garantindo práticas consistentes.
- Redução de custos. A implementação do 5S pode levar à economia de custos por meio da redução dos níveis de estoque, dos custos de manutenção e do tempo de inatividade. Além disso, o aumento da eficiência e da qualidade pode resultar em menos retrabalho e custos de garantia.
- Envolvimento dos funcionários. O envolvimento dos funcionários no processo 5S permite que eles se apropriem de seus espaços de trabalho e processos, o que leva a níveis mais altos de envolvimento, moral e satisfação no trabalho.
- Satisfação do cliente. Os processos simplificados e a qualidade aprimorada resultantes da implementação do 5S podem levar a uma maior satisfação do cliente devido a prazos de entrega mais rápidos, menos erros e maior confiabilidade do produto ou serviço.
Onde aplicar o sistema 5S
Listamos a seguir os setores que podem se beneficiar da aplicação do 5S:
- Fábricas e ambientes de produção. O 5S é comumente aplicado em ambientes de manufatura em que o fluxo de trabalho e a organização eficientes são essenciais. Ao implementar o 5S, as empresas podem reduzir os tempos de preparação, minimizar os defeitos e melhorar a produtividade geral no chão de fábrica.
- Setores de serviços. Embora originalmente desenvolvidos para o setor de manufatura, os princípios do 5S também podem ser aplicados nos setores de serviços, como saúde, hotelaria e bancos. A organização dos espaços de trabalho, a otimização dos processos e a manutenção da limpeza podem melhorar a prestação de serviços, reduzir os tempos de espera e aumentar a satisfação do cliente.
- Escritórios. Os espaços de escritório podem se beneficiar significativamente da implementação do 5S. Ao organizar documentos, suprimentos e estações de trabalho, as empresas podem aumentar a produtividade dos funcionários, reduzir a desordem e criar um ambiente de trabalho mais agradável.
- Armazenamento e logística. A organização e a limpeza eficientes são cruciais nas operações de armazenamento e logística para minimizar erros, melhorar a precisão do inventário e aumentar a segurança. A implementação do 5S pode ajudar a simplificar os processos de coleta, embalagem e expedição, reduzindo o desperdício e melhorando o rendimento.
- Hospitais e instalações de saúde. Em ambientes de saúde, o 5S pode contribuir para a segurança do paciente, o controle de infecções e a eficiência operacional. Estações de trabalho bem organizadas, processos padronizados e limpeza regular podem ajudar os prestadores de serviços de saúde a oferecer um atendimento de melhor qualidade, minimizando os riscos.
- Varejo. Ambientes de varejo, como lojas e depósitos, podem se beneficiar da implementação do 5S para melhorar o gerenciamento de estoque, reduzir o desperdício e aumentar a satisfação do cliente. A organização de mercadorias, a otimização do espaço de armazenamento e a manutenção da limpeza podem levar a operações mais tranquilas e ao aumento das vendas.
Quais perguntas devem orientar cada estágio do 5S?
Ao implementar o conceito 5S como parte da Metodologia Lean, é essencial fazer perguntas críticas em cada estágio para garantir a implementação eficaz e a melhoria contínua. Aqui estão as perguntas que devem acompanhar a implementação de cada etapa da metodologia 5S:
Classificar (Seiri)
- Quais itens são necessários para as operações atuais?
- Quais itens são desnecessários ou redundantes?
- Com que frequência os itens são usados?
- Há algum risco de segurança associado aos itens que estão sendo classificados?
- Podemos reduzir os níveis de estoque sem afetar a produtividade?
Organizar / Colocar em ordem (Seiton)
Qual é o layout mais eficiente para o espaço de trabalho?
Como podemos organizar os itens para minimizar o desperdício de movimento e otimizar o fluxo de trabalho?
Há algum gargalo ou obstáculo no layout atual?
Como podemos comunicar visualmente os locais designados para os itens?
Que soluções de armazenamento são necessárias para manter a ordem e a acessibilidade?
Dar Brilho (Seiso)
Quais são os padrões de limpeza para o espaço de trabalho?
Com que frequência a limpeza deve ser feita?
Há algum risco de segurança ou problema de manutenção que precise ser abordado durante a limpeza?
Como podemos envolver os funcionários na manutenção de um espaço de trabalho limpo e organizado?
Que indicadores visuais podem ser usados para monitorar os níveis de limpeza?
Padronizar (Seiketsu)
Quais são os procedimentos padrão para Classificar, Colocar em Ordem e Dar Brilho?
Como podemos garantir a implementação consistente desses procedimentos?
Que treinamento é necessário para instruir os funcionários sobre os procedimentos padronizados?
Como vamos monitorar a conformidade com os padrões estabelecidos?
Com que frequência os procedimentos devem ser revisados e atualizados?
Sustentar (Shitsuke)
Como podemos promover uma cultura de melhoria contínua e propriedade?
Que treinamento e suporte são necessários para manter as práticas de 5S?
Como reconheceremos e recompensaremos os funcionários por manterem os padrões de 5S?
Que mecanismos serão implementados para incentivar o envolvimento e a participação dos funcionários?
Como vamos medir a eficácia de longo prazo da implementação do 5S?
5S: Passo a passo para implementar a metodologia
Aqui trazemos um guia passo a passo para uma empresa implementar o conceito 5S, que faz parte da Metodologia Lean. Seguindo essas etapas e reforçando regularmente os princípios do sistema 5S, é possível obter melhorias sustentáveis na organização e na eficiência do local de trabalho, o que vai impactar positivamente a qualidade, a segurança e a satisfação dos colaboradores.
Confira a seguir o passo a passo do 5S:
Etapa 1: Classificar (Seiri)
Objetivo: Eliminar itens desnecessários e manter apenas o que é essencial.
- Realize uma avaliação completa do espaço de trabalho, identificando todos os itens, ferramentas e materiais.
- Classifique os itens em categorias essenciais e não essenciais.
- Remova os itens desnecessários do espaço de trabalho, realocando ou descartando o que não serve mais.
- Rotule e marque claramente os itens para indicar sua finalidade e local de armazenamento.
Resultado:
- Redução da desordem e melhor controle visual.
- Aumento da eficiência, pois os funcionários podem encontrar facilmente os itens necessários.
- Identificação de equipamentos obsoletos ou redundantes, reduzindo a necessidade de espaço de armazenamento.
Etapa 2: Colocar em ordem (Seiton)
Objetivo: Organizar os itens essenciais para facilitar o acesso e a eficiência.
- Defina locais específicos para cada item com base na frequência de uso e no fluxo de trabalho.
- Organize as ferramentas e os materiais em uma ordem lógica, garantindo a fácil recuperação e devolução.
- Use indicadores visuais, como etiquetas, código de cores e outros tipos de marcadores para orientar a organização.
- Implemente soluções de armazenamento como prateleiras, estantes ou armários para manter a ordem.
Resultado:
- Fluxo de trabalho simplificado e tempos de busca reduzidos.
- Melhor organização e acessibilidade, o que leva ao aumento da produtividade.
- Identificação clara de ferramentas ou equipamentos ausentes por meio do gerenciamento visual.
Etapa 3: Dar Brilho (Seiso)
Objetivo: Limpar e manter um espaço de trabalho seguro e organizado.
- Desenvolva um cronograma de limpeza regular para o espaço de trabalho e os equipamentos.
- Treine os funcionários sobre os procedimentos e responsabilidades de limpeza.
- Identifique e resolva os riscos de segurança, vazamentos ou problemas de funcionamento durante a limpeza.
- Implemente controles visuais para monitorar os níveis de limpeza.
Resultado:
- Aumento da segurança no local de trabalho e redução de acidentes.
- Aumento da confiabilidade e da vida útil do equipamento.
- Criação de um ambiente de trabalho positivo.
Etapa 4: Padronizar (Seiketsu)
Objetivo: Estabelecer procedimentos consistentes para manter os três primeiros "S"s (Seiri, Seiton, Seiso).
- Desenvolva procedimentos operacionais padrão (SOPs) para Classificar, Colocar em Ordem e Dar Brilho.
- Treine os funcionários sobre os procedimentos padronizados e as expectativas.
- Implemente auditorias regulares para garantir a conformidade com os padrões estabelecidos.
- Revise e atualize continuamente os procedimentos, conforme necessário.
Resultado:
- Melhorias consistentes e sustentadas.
- Redução da variação nos processos, levando a uma maior confiabilidade.
- Integração mais fácil para novos funcionários.
Etapa 5: Sustentar (Shitsuke)
Objetivo: Desenvolver uma cultura de melhoria contínua e de propriedade (ownership), em que os colaboradores se sentem responsáveis.
- Promova uma mentalidade de melhoria contínua entre os funcionários.
- Implemente programas de treinamento e workshops sobre os princípios do 5S.
- Estabeleça sistemas de reconhecimento e recompensa pela manutenção dos padrões 5S.
- Incentive discussões regulares da equipe para identificar e abordar oportunidades de melhoria.
Resultado:
- Adesão de longo prazo aos princípios da metodologia 5S.
- Melhoria contínua da eficiência e da eficácia.
- Aumento do moral e do envolvimento dos funcionários.
Exemplos de empresas que aplicam o 5S
Desde o seu surgimento e popularização, o método 5S foi adotado por empresas de diferentes segmentos para resolver problemas comuns, como ineficiências, desperdício, riscos à segurança e problemas de qualidade. Ao adotar os princípios de Classificar, Colocar em Ordem, Dar Brilho, Padronizar e Sustentar, essas empresas obtiveram melhorias significativas em produtividade, segurança, qualidade e na maneira com que os colaboradores se sentem em relação a seu trabalho e à empresa.
Veja a seguir exemplos de empresas que adotaram o sistema 5S e os problemas que resolveram, juntamente com os resultados obtidos:
Toyota Motor Corporation
A Toyota é uma das pioneiras em manufatura enxuta e é conhecida por sua implementação do sistema 5S. Ao implementar o 5S, a Toyota resolveu vários problemas, como ineficiências nos processos de produção, desperdício de tempo e recursos devido a espaços de trabalho desorganizados e inconsistências na qualidade. Como resultado, a Toyota obteve melhorias significativas na produtividade, na segurança e na qualidade dos produtos. A empresa também registrou redução nos prazos de entrega e aumento do moral dos funcionários devido a ambientes de trabalho mais limpos e organizados.
Boeing
A Boeing, gigante do setor aeroespacial, utilizou o sistema 5S para melhorar a eficiência e a segurança em suas fábricas. Antes de implementar o 5S, a Boeing enfrentava desafios como a má administração de estoques, o mau posicionamento de ferramentas e riscos à segurança devido à desorganização das áreas de trabalho. Ao implementar os princípios do 5S, a Boeing padronizou seus processos, reduziu o desperdício e melhorou a segurança no local de trabalho. Isso resultou em fluxos de produção simplificados, tempos de resposta mais rápidos e maior qualidade do produto.
General Electric (GE)
A GE é outro exemplo de empresa que implementou com sucesso o sistema 5S em suas várias divisões. Antes de adotar o 5S, a GE enfrentava problemas como tempo de inatividade dos equipamentos devido a práticas de manutenção ruins, dificuldade de localizar ferramentas e materiais e variabilidade nos processos de fluxo de trabalho. Com a metodologia 5S, a GE conseguiu eliminar o desperdício, melhorar a confiabilidade dos equipamentos e aumentar a eficiência operacional geral. Isso levou à redução dos custos de produção, ao aumento do rendimento e ao maior envolvimento dos funcionários.
Nestlé
A Nestlé, uma empresa global de alimentos e bebidas, implementou o sistema 5S em suas instalações de fabricação para otimizar os processos e garantir os padrões de segurança alimentar. Antes da implementação do 5S, a Nestlé enfrentava desafios como riscos de contaminação cruzada, manuseio ineficiente de materiais e dificuldades para manter os padrões de limpeza. Ao adotar os princípios do 5S, a Nestlé padronizou as práticas de trabalho, estabeleceu controles visuais claros e melhorou os procedimentos de saneamento. Isso resultou no aumento da qualidade do produto, na conformidade com os requisitos regulatórios e na redução dos custos operacionais.
A implementação efetiva do sistema 5S pode transformar radicalmente qualquer ambiente de trabalho industrial. Além de promover um ambiente mais seguro e eficiente, o 5S ajuda a cultivar uma cultura de trabalho disciplinada e engajada. Convidamos as organizações a adotar essas práticas para não apenas melhorar a operacionalidade, mas também para impulsionar a satisfação e a produtividade dos funcionários.
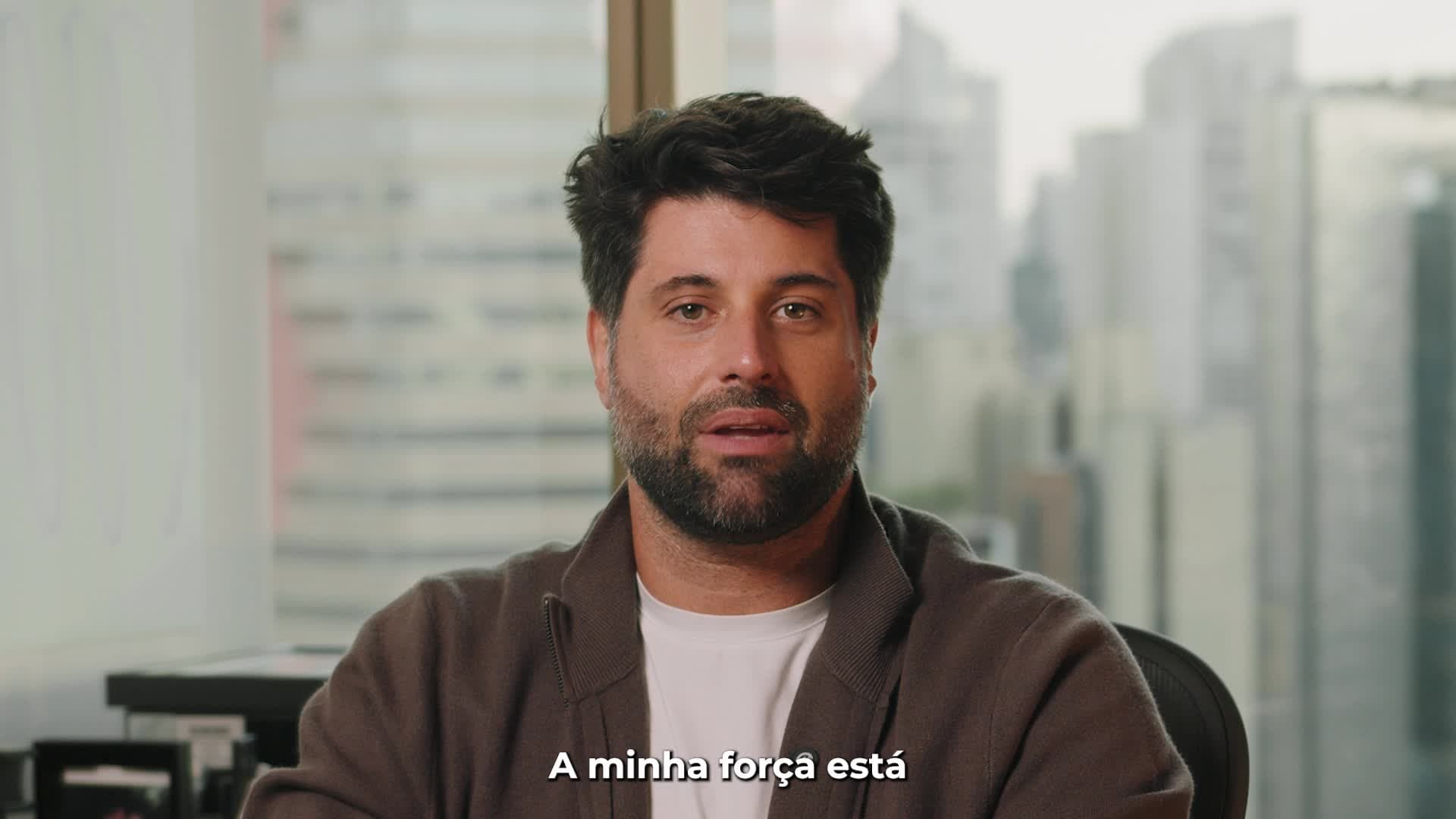
G4 Gestão e Estratégia
Lidere o seu negócio e supere desafios com técnicas e práticas usadas pelas empresas que mais crescem no mundo.
Garanta a sua vagaColunistas
Tallis Gomes
Fundador, mentor, sócio e ex-CEO do G4 Educação, fundador e ex-CEO da Singu e fundador e ex-CEO da Easy Taxi.
Maria Isabel Antonini
Engenheira Industrial de formação, especialista em finanças, sócia e CEO do G4 Educação.
Alfredo Soares
Fundador e mentor do G4 Educação e presidente da Loja Integrada.